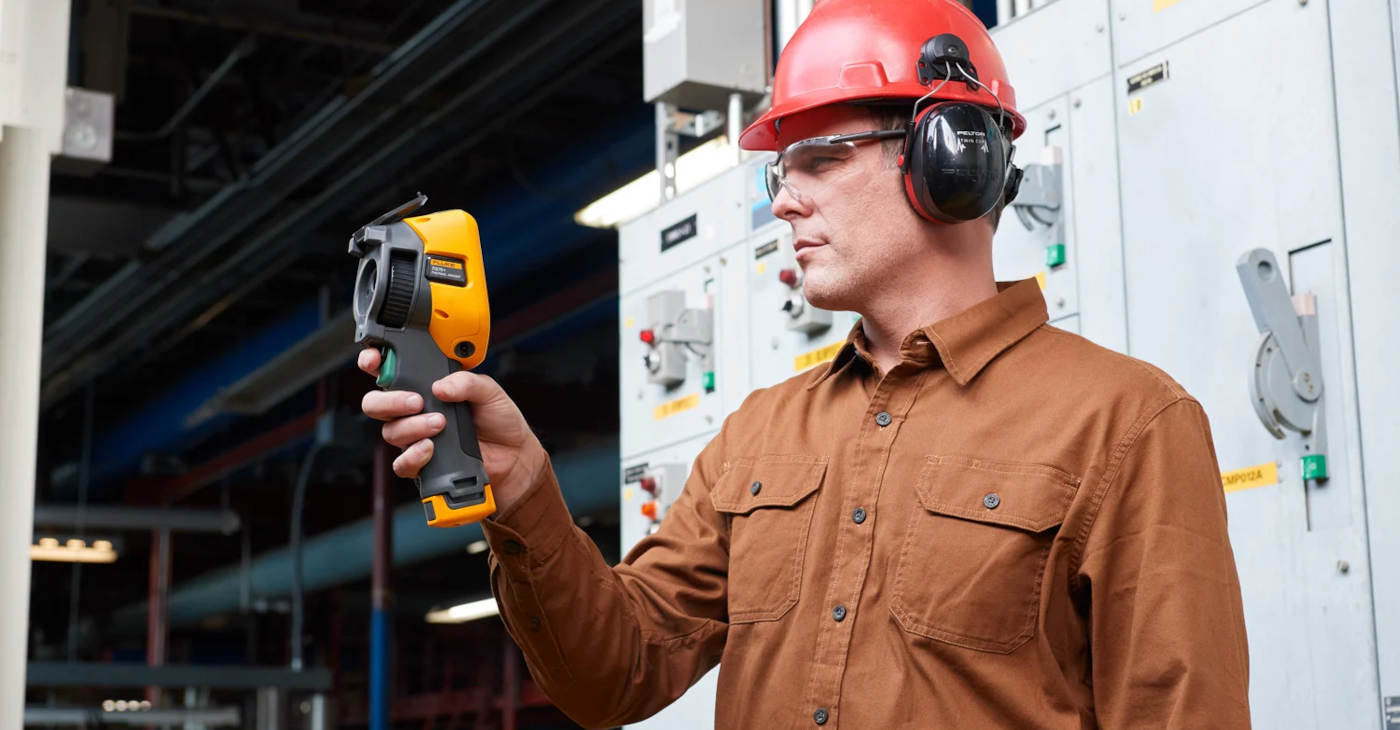
12 Nov Uso de cámaras termográficas en inspecciones eléctricas para optimizar el mantenimiento preventivo y la seguridad
La termografía infrarroja se ha convertido en una herramienta clave en las inspecciones eléctricas industriales, ya que permite detectar problemas potenciales de forma temprana y reducir los costes de mantenimiento y reparación. En circuitos trifásicos industriales, las cámaras termográficas son capaces de identificar diferencias de temperatura anómalas que pueden revelar problemas como desequilibrios de fase o conexiones sueltas.
Tabla de contenidos
Con una inspección regular y el uso de herramientas avanzadas como las cámaras termográficas de Fluke, los técnicos pueden llevar a cabo un monitoreo preciso y eficiente de los equipos eléctricos, lo que no solo previene fallos, sino que también garantiza un rendimiento óptimo.
El Poder de la Termografía Infrarroja en Inspecciones Eléctricas
Las cámaras termográficas permiten visualizar gradientes térmicos en circuitos y componentes eléctricos, identificando los puntos calientes que pueden ser indicativos de problemas. Las cámaras de Fluke, como la Fluke TiS75+, combinan imágenes infrarrojas y de luz visible (tecnología IR-Fusion) para proporcionar una visualización dual. Esta capacidad de fusión permite una identificación precisa de los problemas mediante la alineación exacta de las imágenes térmicas y visibles a cualquier distancia. Esta tecnología facilita la identificación de puntos críticos, como contactos flojos o desequilibrios de fase, que pueden tener efectos graves en el sistema eléctrico si no se detectan y corrigen a tiempo.
Desequilibrio de Fases y sus Efectos en el Sistema Eléctrico
El desequilibrio de fases se produce cuando las tensiones y/o las corrientes en las fases de un sistema trifásico no son iguales. El desequilibrio de las corrientes en un sistema trifásico es una de las causas más comunes de sobrecalentamiento. Este desequilibrio puede deberse a problemas de suministro, baja tensión, fallos en la resistencia de aislamiento de las bobinas del motor o un incorrecto reparto de cargas en las fases. Si el desequilibrio es grave, puede sobrecargar la instalación y provocar el fallo de componentes críticos.
La fase sobrecargada por desequilibrio experimentará una mayor pérdida por calor, pues esta pérdida crece rápidamente con la intensidad (P= I²R). Este sobrecalentamiento puede deteriorar las conexiones y causar fallos prematuros en motores y cargas conectadas. Si el exceso de calor resulta en un aumento de la resistencia del circuito, el efecto de sobrecalentamiento se agravará todavía más, pues es proporcional a la resistencia eléctrica (de nuevo, P= I²R)
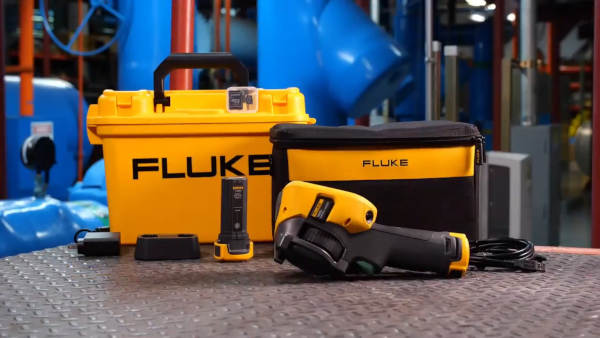
Componentes Críticos para las Inspecciones de Termografía
Durante una inspección, los técnicos deben capturar imágenes térmicas de los cuadros eléctricos y otros puntos de alta carga, como variadores de velocidad, controles y desconexiones. La inspección debe realizarse cuando los equipos están en plena operación para obtener una imagen precisa de las condiciones reales. Las cámaras termográficas de Fluke son ideales para esta tarea, ya que permiten registrar las temperaturas y almacenarlas en un ordenador para compararlas con mediciones futuras. Este procedimiento ayuda a establecer un historial térmico y a detectar cambios en el tiempo, lo que facilita la predicción y prevención de fallos.
Interpretación de las Imágenes Térmicas para Diagnosticar Problemas
La interpretación de los termogramas requiere que los técnicos identifiquen patrones térmicos básicos. Por ejemplo, una alta resistencia debido a un contacto defectuoso suele reflejarse en puntos de calor concentrados. En el caso de desequilibrios de fase o sobrecargas, los patrones de temperatura se distribuirán de manera desigual entre las fases. La cámara termográfica permite observar estos patrones y determinar las áreas que requieren atención inmediata. Algunos ejemplos de problemas comunes incluyen conexiones sueltas en fusibles y puntos de contacto defectuosos en cuadros eléctricos, que provocan un aumento de temperatura considerable.
Normativas y Umbrales de Temperatura para la Seguridad
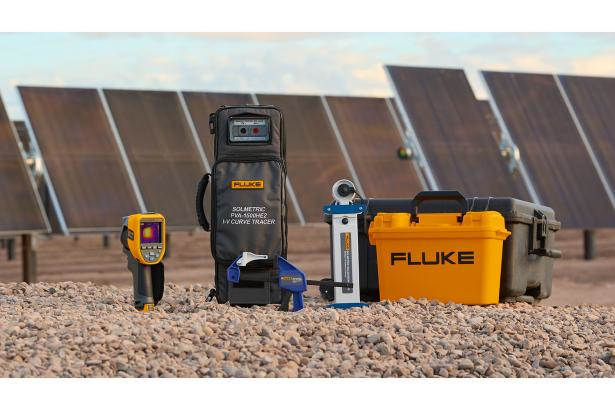
Las normativas de la InterNational Electrical Testing Association (NETA) recomiendan la acción inmediata cuando la diferencia de temperatura entre componentes similares en condiciones similares excede los 15 °C. La temperatura del equipo también debe compararse con el aire ambiente: si la diferencia supera los 40 °C, se debe investigar el problema y realizar las reparaciones necesarias. Las cámaras termográficas son una herramienta ideal para estas inspecciones, ya que permiten una evaluación precisa sin contacto directo.
Según la Asociación Nacional de Fabricantes Eléctricos (NEMA), los desequilibrios de tensión pueden calcularse como un porcentaje de desviación en comparación con la tensión promedio y deben mantenerse dentro de los límites recomendados para evitar daños. Esta Asociación sugiere que los motores no operen con un desequilibrio de tensión superior al 1%. Esta limitación se aplica de manera específica a los motores, aunque otros equipos pueden requerir otros parámetros.
Prácticas para Maximizar la Eficiencia y la Seguridad
Para maximizar la efectividad de las inspecciones termográficas, el sistema debe estar cargado durante la inspección, preferentemente en un nivel de al menos el 40% de su capacidad nominal. Esto permite detectar mejor los problemas derivados de sobrecargas y fallos en las conexiones. También es esencial abrir las carcasas eléctricas cuando sea seguro y posible, para obtener una lectura directa de los circuitos y no limitar la inspección a las temperaturas de la superficie exterior.
Ventajas del Monitoreo Continuo para la Prevención de Fallos
El monitoreo continuo mediante cámaras termográficas permite reducir considerablemente los costos de mantenimiento, al identificar problemas antes de que provoquen daños significativos. Por ejemplo, un motor que falla debido a un desequilibrio puede generar pérdidas importantes en términos de reemplazo, producción y tiempo de inactividad. Si se estima que el coste de reemplazar un motor de 50 CV asciende a 5.000 euros, con pérdidas adicionales por tiempo de inactividad de hasta 24.000 euros, el impacto total de un fallo inesperado puede superar los 29.000 euros anuales.
Con la ayuda de herramientas avanzadas como las cámaras termográficas Fluke, los técnicos pueden realizar un seguimiento exhaustivo y regular de la condición de los equipos eléctricos. Al registrar cada inspección en informes detallados, que incluyan imágenes térmicas y digitales, las empresas pueden asegurar una comunicación efectiva de los problemas y tomar decisiones informadas sobre las reparaciones necesarias.
Inversión en Inspección Termográfica para la Eficiencia y Seguridad Eléctrica
El uso de cámaras termográficas en inspecciones eléctricas es una inversión en eficiencia, seguridad y ahorro. Al integrar esta tecnología en un plan de mantenimiento preventivo, las empresas pueden reducir el riesgo de fallos catastróficos, extender la vida útil de sus equipos y mejorar la seguridad de las instalaciones. Con herramientas avanzadas como la Fluke TiS75+, los técnicos tienen en sus manos un recurso de diagnóstico preciso que facilita la identificación temprana de problemas y asegura un rendimiento óptimo en los sistemas eléctricos industriales.
No hay comentarios